ام اس دی اس متیل الکل
ام اس دی اس مواد (msds) : ام اس دی اس متیل الکل
سایز (ام اس دی اس) مواد (msds) | کد سایز(ام اس دی اس) مواد (msds) |
--- |
------ |
30*25 | M |
50*45 | N |
70*50 | L |
100*70 | B |
نوع جنسام اس دی اس مواد (msds) | کد جنس ام اس دی اس مواد (msds) |
برچسب روزرنگ | D |
برچسب شبرنگ | R |
برچسب شبنما | P |
جنس زمینه زیرام اس دی اس مواد (msds) | کد زمینهام اس دی اس مواد (msds) |
روزرنگ /گالوانیزه /پی وی سی | G |
شبرنگ/گالوانیزه /پی وی سی | H |
شبنما /گالوانیزه /پی وی سی | Z |
سایز سفارشی MSDS هم پذیرفته می شود .
متیل الکل (متانول، الکل متیلیک، کاربینول) یک ترکیب شیمیایی با فرمول CH3OH و سادهترین نوع الکل است. متانول مایعی سبک، فرار، بدون رنگ و قابل اشتعال می باشد.
متانول خالص اولین بار در سال 1661 توسط رابرت بویل از تقطیر چوب به دست آمد. در سال 1923 شیمیدان آلمانی به نام آلوین میتاش (Alwin Mittasch) در حین پژوهش درباره سنتز آمونیاک متوجه تشکیل شدن ترکیبات اکسیژن دار شد. ادامه تحقیقات وی منجر به تهیه متانول از گاز سنتز (مخلوطی از هیدروژن (H2) و کربن مونوکسید (CO) به دست آمده از کک)، شد و اختراعی را در 12 ژانویه سال 1926 به ثبت رساند. این واکنش با استفاده از کاتالیزورهای کروم-روی در شرایط بسیار سختی از جمله فشار 1000-300 اتمسفر و دمایی در حدود 400 درجه سانتیگراد انجام می شد. امروزه به منظور تولید متانول، از کاتالیزگرهای با کارایی بهتر و موثرتر که در فشارهای پایین عمل می کنند استفاده می گردد. این کاتالیزگرها شامل مخلوطی از مس و اکسید روی و آلومینیوم می باشند که منجر به انجام واکنش در فشار 100-50 اتمسفر و دمایی در حدود 250 درجه سانتیگراد می شوند.
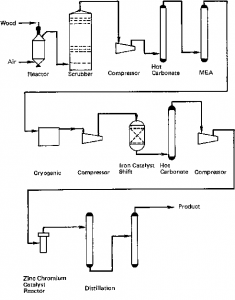
فرآیند تولید متانول
1- آماده سازی خوراک
گاز طبیعی و دی اکسید کربن در فشارهای متفاوت به مجتمع تولیدی وارد شده و هر یک در کمپرسورهای گریز از مرکز جداگانه ای تا فشار مورد نظر فرآیند، متراکم و مخلوط می گردند. این واحد شامل سیستم های متراکم کننده و تصفیه گازهای خوراک ورودی به شرح زیر می باشد.
تراکم گاز طبیعی
گاز طبیعی ورودی طی دو مرحله در کمپرسور مربوطه از فشار حدود 11bar تا فشار 45bar متراکم می گردد. سیستم تراکم گاز طبیعی را کمپرسور، خنک کننده میانی و مخازن آبگیری تشکیل می دهند. نیروی محرکه مورد نیاز کمپرسور گاز طبیعی را از طریق توربین تأمین می کنند.
تراکم دی اکسید کربن
دی اکسید کربن تولیدی در واحد الفین با فشار اتمسفریک به واحد تولید متانول وارد می شود. به منظور متراکم نمودن این گاز تا فشار 45bar از یک کمپرسور سه مرحله ای بهره می گیرند. سیستم تراکم دی اکسید کربن شامل کمپرسور، خنک کننده های میانی، بخش آبگیری و همچنین خنک کننده گاز برگشتی می باشد. نیروی محرکه این بخش نیز توسط توربین بخار تامین می شود.
تصفیه گاز خوراک
پس از این که گاز طبیعی و کربن دی اکسید هم فشار شدند با یکدیگر مخلوط شده و به منظور حذف ناخالصی های موجود که عمدتاً شامل هیدروژن سولفید (H2S)، ترکیبات آلی گوگرددار و همچنین ترکیبات آلی کلردار می باشند، پس از گرم شدن در قسمت بازیافت حرارت ریفرمر اول و رسیدن به دمای 350 درجه سانتی گراد، به ترتیب وارد رآکتورهای دی سولفوریزاسیون می شوند و در حضور کاتالیزور کبالت-مولیبدن، ترکیبات آلی گوگردی و کلردار به ترتیب به گازهای H2S و HCl تبدیل می شوند. سپس هیدروکلریک اسید موجود در گازهای خروجی این مرحله با عبور از رآکتورهای دکلریناسیون جذب کاتالیزور سدیم آلومینات شده و به منظور جذب هیدروژن سولفید به رآکتورهای جذب H2S که حاوی کاتالیزور اکسید روی (ZnO) می باشد، منتقل می گردند.
2- تولید گاز سنتز (واحد ریفرمینگ)
با عبور مخلوط خوراک گاز و آب از بستر کاتالیزور اکسید نیکل واکنش ریفرمینگ گاز سنتز صورت می گیرد. واحد ریفرمینگ شامل قسمت های زیر است:
اشباع سازی
بخشی از بخار آب که مورد نیاز واحد ریفرمینگ است در قسمت اشباع سازی تأمین می گردد. در این قسمت بخش اعظم گاز خوراک خروجی از رآکتورهای گوگردزدایی در یک برج با آب مجاور شده و در نتیجه انتقال جرم، میزان بخار آب موجود در گاز تا حد اشباع افزایش می یابد. واحد اشباع سازی شامل برج اشباع سازی و پمپ های سیرکولاسیون آب است، آب ورودی به سیستم اشباع در چرخه سنتز به دمای مورد نظر رسانده می شود. بخش عمده بخار مورد نیاز ریفرمینگ در قسمت اشباع سازی تأمین شده و مابقی بصورت جریان بخار تزریق می گردد.
ریفرمینگ اولیه
مخلوط گاز خوراک و بخار خروجی از واحد اشباع سازی، پس از گرم شدن تا دمای 500 درجه سانتی گراد در گرمکن گاز خوراک که در بخش بازیافت حرارت ریفرمر تعبیه شده، از طریق یک شبکه توزیع، به تیوب های ریفرمر اولیه که حاوی کاتالیزور های اکسید نیکل است، وارد می شود. واکنش های این بخش گرماگیر بوده لذا انرژی مورد نیاز خود را از طریق مشعل های تعبیه شده در سقف ریفرمر تأمین می نماید. فشار عملیاتی ریفرمر حدود 37bar بوده و دمای گاز خروجی از آن حدود 800 درجه سانتی گراد است.
دود حاصل از احتراق مشعل های ریفرمر به منظور بازیافت حرارت به قسمت بازیافت حرارت ریفرمر که به نوبه خود شامل فوق گرمکن های بخار، پیش گرمکن های گاز خوراک، گرم کننده گاز ورودی به رآکتورهای گوگردزدایی و پیش گرمکن هوای احتراق می باشد، هدایت می گردد.
ریفرمینگ ثانویه
گاز خروجی از ریفرمر اول پس از مخلوط شدن با باقیمانده گاز خروجی از قسمت گوگردزدایی به ریفرمر دوم هدایت می شود. اکسیژن خالص تولید شده در دستگاه تولید اکسیژن، پس از گرم شدن در پیش گرمکن بخاری به ریفرمر دوم وارد گشته و در اثر مخلوط شدن اکسیژن و گاز، عمل احتراق صورت گرفته و دما در قسمت بالایی ریفرمر دوم تا 1500 درجه سانتی گراد افزایش می یابد. مخلوط گرم حاصل از روی بستر کاتالیزور اکسید نیکل عبور کرده و در این مرحله ادامه واکنش های ریفرمینگ صورت می پذیرد.
دما و فشار گاز خروجی از ریفرمر دوم به ترتیب 1020 درجه سانتی گراد و 35bar می باشد که به منظور سرد کردن به سیستم حرارت گاز ریفرمر شده هدایت می شود. سیستم بازیافت حرارت گاز ریفرمر شده را مولد های بخار، پیش گرمکن آب، ری بویلرهای برج تقطیر و پیش گرمکن آب بدون املاح تشکیل می دهند.
گاز سنتز تولید شده در نهایت به خنک کننده نهایی و مخزن آبگیر هدایت شده و دمای آن تا 50 درجه سانتی گراد کاهش می یابد. میعانات بخار حل شده پس از جمع آوری در مخازن آبگیر، به منظور حذف کربن دی اکسید حل شده در آن فرآوری می گردد و جهت استفاده دوباره به سیستم تهیه آب بدون املاح هدایت می شود.
3- تراکم گاز سنتز
گاز سنتز خروجی از مخازن آبگیر، به منظور تراکم تا فشار 73bar به کمپرسور گریز از مرکز گاز سنتز هدایت می شود. نیروی محرکه این کمپرسور از توربین بخار تأمین می گردد.
4- سنتز متانول
سنتز متانول در حضور کاتالیزور مس-روی در فشار حدود 70bar و دمایی در حدود 220 درجه سانتی گراد صورت می پذیرد. واکنش های فوق تعادلی بوده و لذا با عبور گاز سنتز از بستر کاتالیزور، تنها بخشی از ترکیبات موجود در گاز سنتز وارد واکنش شده و باقیمانده بدون تغییر از رآکتور خارج می شوند. بنابراین برای تولید حداکثری متانول، می بایست متانول موجود در گاز خروجی از رآکتور جدا شده و باقیمانده گاز مجدد به رآکتور بازگردانده شود که به این منظور از چرخه سنتز متانول استفاده می شود. چرخه سنتز متانول شامل رآکتورهای سنتز، سیرکولاتور، خنک کننده های هوایی، خنک کننده های آبی، مخازن جداکننده متانول خام، پیش گرمکن های آب سیستم اشباع و مبدل های گازی گرم کننده خوراک رآکتور می باشد. گاز خروجی از کمپرسور سنتز به دو بخش تقسیم شده که بخش اول پس از مخلوط شدن با گاز خروجی از مخزن و گرم شدن در مبدل به رآکتور هدایت می شود. گاز خروجی از رآکتور سنتز، در خنک کننده هوایی و خنک کننده آبی تا دمای 45 درجه سانتی گراد خنک شده و طی آن متانول موجود در گاز، تبدیل به مایع شده و در مخرن جداکننده متانول خام از گاز جدا می گردد.
گاز خروجی از مخزن جداکننده متانول خام، پس از مخلوط شدن با بخش دوم گاز خروجی از کمپرسور به سیرکولاتور هدایت شده و از آن مسیر به منظور تبادل حرارت با گازهای گرم خروجی از رآکتور سنتز و رسیدن به دمای لازم برای واکنش به مبدل وارد شده و از آنجا به رآکتور سنتز هدایت می گردد. متانول خام جدا شده در مخازن جداکننده متانول خام، پس از کاهش فشار تا حدود 7bar به برج تقطیر هدایت می شود و به دلیل کاهش فشار، دی اکسید کربن حل شده در آن آزاد می گردد.
5- تصفیه متانول
پس از جدا سازی دی اکسید کربن، متانول خام گرم شده و براي جداسازی ترکیبات سبک به برج تقطیر هدایت می گردد. انرژی مورد نیاز تقطیر توسط ری بویلر گازی و ری بویلر بخار تأمین می شود. سیستم جریان برگشتی این برج شامل خنک کننده هوایی، خنک کننده آبی، مخزن جمع آوری کندانس و پمپ جریان برگشتی می باشد. متانول عاری از ترکیبات سبک به منظور جداسازی آب موجود در آن و رسیدن به خلوص 99/9 درصد به برج تخلیص در فشار 7/5bar هدایت می گردد.
انرژی مورد نیاز تقطیر در این برج از طریق ری بویلر گازی و ری بویلر بخاری تأمین می شود. بخاری که در بالاترین سینی این برج جمع آوری می شود متانول خالص بوده که پس از میعان در کندانسور آبی، به قسمت ذخیره سازی هدایت می گردد. بخارات خروجی از آخرین سینی این برج پس از تأمین انرژی تقطیر در ری بویلر، مایع شده و پس از جمع آوری در مخزن برگشتی به وسیله پمپ به برج تخلیص بازگردانده می شود. مخلوط آب و متانول خروجی از پائین برج به برج تقطیر بعدی منتقل می شود و انرژی مورد نیاز تقطیر آن از طریق ری بویلر تأمین می گردد.
6- سامانه بخار و کندانس
بخار مورد نیاز واحد متانول در فشار 114bar در مبدل های بازیافت حرارتی و بویلرهای کمکی تولید می شود. بخار 114bar به منظور رانش توربین و توربین کمپرسور در واحد تولید اکسیژن مصرف می شود.
7- ذخیره سازی و بارگیری
متانول خام تولید شده پس از جداسازی کربن دی اکسید به مخزن ذخیره ای با ظرفیت تولید و نگهداری متانول تا 24 ساعت وارد شده و با کمک پمپ هایی متانول خام به پیش گرمکن بازگردانده می شود. متانول خالص تولید شده پس از خنک شدن وارد مخازن نگهداری متانول شده و به وسیله پمپ انتقال محصول به مخازن ذخیره اصلی هدایت می گردند.
کاربردهای متانول
1- متانول به عنوان حلال و ضد یخ کاربرد وسیعی دارد.
2- در تهیه فرمالدهید به منظور تولید رزین های مربوطه مورد استفاده قرار می گیرد.
3- در تهیه استیک اسید به عنوان ماده اولیه مورد استفاده قرار می گیرد.
4- در سوخت های هیدروژنی و همچنین به عنوان جایگزینی در سوخت اتومبیل ها مورد استفاده قرار می گیرد.
5- در تولید اتیلن و پروپیلن به عنوان ماده اولیه صنایع پتروشیمی
نکات ایمنی درباره متانول
متانول ترکیبی بسیار سمی بوده و محصول متابولیت آن، فرمیک اسید و فرمالدئید می باشد که موجب نابینایی و مرگ می شود. متانول می تواند از طریق تنفس و یا جذب از راه پوست وارد بدن شود. لازم به ذکر است که به طور مداوم در معرض متانول بودن بدون استفاده از لوازم محافظت کننده (مانند ماسک) خطرناک است.
متانول پس از مصرف، مانند اتانول، در عرض 30 تا 60 دقيقه به حداكثر سطح پلاسمايی خود می رسد. بدون درمان، سطح كشنده آن 1/25 سانتی متر مکعب بر کیلوگرم و یا یک گرم بر کیلوگرم و دوز مسبب کوری حداقل 24 گرم یل 30 میلی لیتر است.
كوری ناشی از متانول به دلیل توليد موضعی فرمالدئيد در شبکيه و آسيب عصب بينايی اتفاق می افتد.
ساده ترین روش تشخیص متانول از اتانول
بسیاری از پارامترهای فیزیکی و شیمیایی متانول و اتانول به هم نزدیک می باشد، لذا تشخیص این دو الکل از یکدیگر بدون استفاده از تجهیزات آزمایشگاهی کار ساده ای نیست. در اینجا قصد ارائه روش های مرسوم برای تشخیص این دو الکل از یکدیگر را نداریم و تنها به اختلاف رنگ شعله آن ها هنگام سوختن در یک ویدئو اشاره خواهیم نمود.
دقت داشته باشید که هیچ روش امنی برای تشخیص متانول از اتانول در منزل وجود ندارد.
نوشتن نظر
نام شما:نظر شما: توجه : HTML ترجمه نمی شود!
رتبه: بد خوب
کد امنیتی را در کادر زیر وارد نمایید: